Pure Gold is not found in nature. It is mined in ores and extracted from gold-bearing veins. One of the active methods gold mining - heap leaching of gold.
Heap leaching is the most cost-effective method of extracting gold from ore. Geography of application of the method
Heap leaching process gold is considered environmentally safe, highly profitable, so it is successfully used by countries in Europe, America and Southeast Asia. Despite the simplicity in application, the technology is carried out using modern tools and requires clear step-by-step instructions.
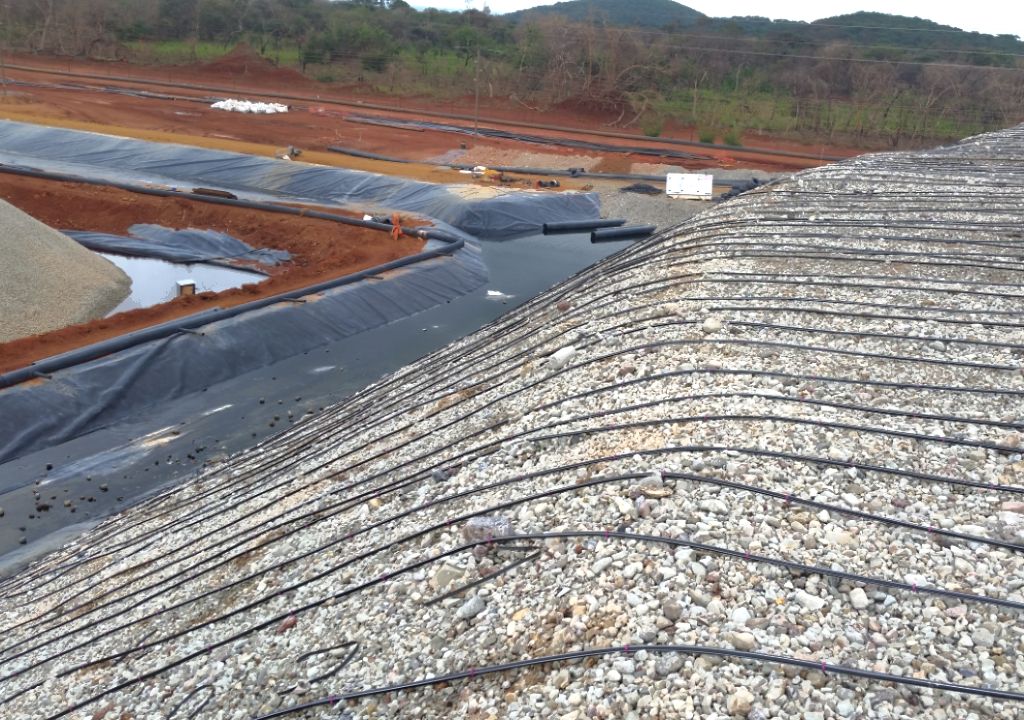
The leaching method is the treatment of gold-bearing ores with special solutions. All the chemical elements begin to interact with each other, and the electrophysical processesThe gold is leached in certain compositions and is further processed through filters. The pure metal is obtained in the last step by electrolysis.
Technology of the gold leaching process
To produce the process heap leaching, it is necessary to prepare a site and an underlying pad. The latter is necessary to hold the solution inside the area where the process will take place. It is necessary to make calculations in order to gold-containing the stack was held within the specified parameters.
Project planning and preliminary calculations
When planning gold mining through heap leaching, we need to consider the factors that determine the success of the project.
- Plan drilling programs. Test the area where the technology is planned to be applied.
- Compare with similar projects.
- Determine what impurities are in the ore. This will help you understand how long the leaching will last and what the level of gold will be.
- Identify the type of ore.
- Determine the gold and silver content.
- Decide on the method of building a pile: it is better to refer to the experience of colleagues.
- Create a reliable testing ground for the work.
- Hire the necessary specialists.
- Strictly supervise the work.
- Conduct test work and analyze the results.
In addition, you should be prepared for unforeseen results. The weather may change, contractors may fail. The characteristics of the ore may also change. It is important to calculate the financial costs and profits, to calculate the possible risks at each stage of the work.
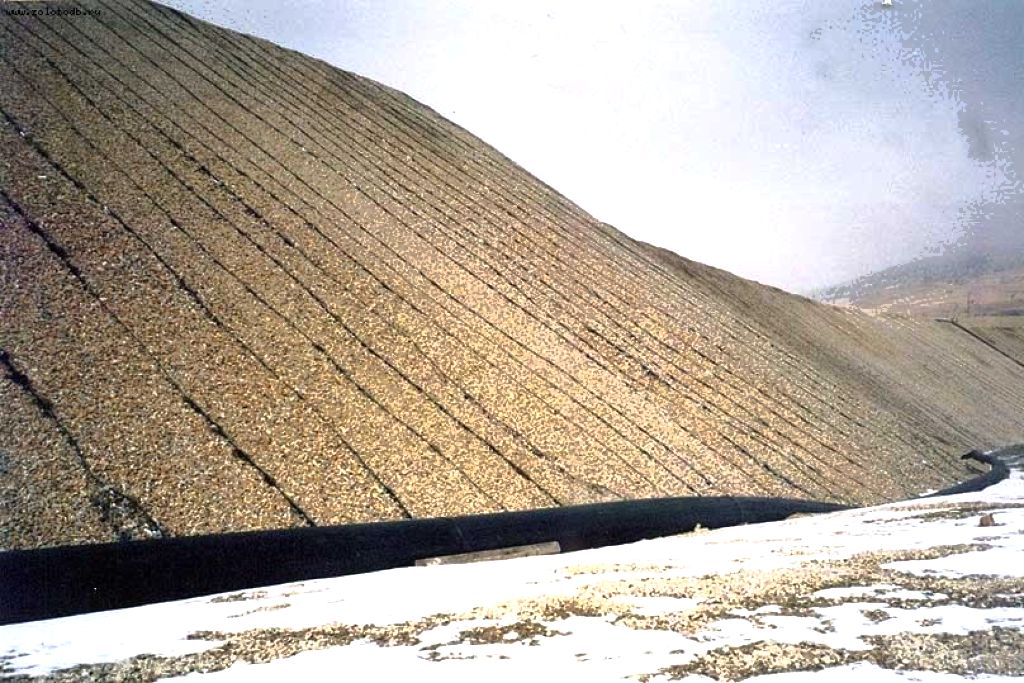
Raw material requirements and ore preparation
Technology is mostly applicable to the processing of low-grade ores, gold mines small sizes. Sands, porous ores have a structure suitable for processing solutions seeped to the gold particles.
Approximately 50% to 90% of gold can be extracted by leaching from oxidized ores, from waste rock dumps. It is practically impossible to obtain precious metal by heap leaching from ores containing sulfides, e.g., with thiourea, sorption-active carbonaceous substances.
To process a gold mine, depending on the amount of gold contained, its composition and filtration properties, the following methods are used:
- Crushing. The leaching process requires fine gold. The ore is crushed to a particle size of 5-20 mm. Sometimes pieces up to 100 mm in size are allowed in the process.
- Screening is the sifting of ore to separate ore elements into size classes. The ore is sieved repeatedly, and the ore is crushed and crushed in between. In some cases, this step may be unnecessary and omitted.
- Shaking of clayey ores with rocky ores. Clay substances clog up the loose structure, interfere with the penetration of solutions to the gold particles, thereby making leaching more difficult. Therefore it is necessary to preliminarily burden the ore by adding cement, alkali, and lime. Some companies use these substances separately.
- Pelletizing of small and finely dispersed fractions. Dusty substances are turned into lumps: briquettes or pellets. In the future, the resulting material is easier to subject to firing.
Also, the preparation of ore for gold leaching includes the construction of a landfill.
Construction of the site in the open air. Basic requirements
Heap leaching technology is carried out in the open air. For this purpose special polygons are equipped, creating favorable conditions.
Preparation of the waterproofing layer
Waterproofing is the most important step in site preparation. To make the landfill watertight, it is concreted, asphalted, or covered with a layer of compacted clay. Often a cheaper method of waterproofing is used - covering the site with synthetic film. Of modern shelters - geomembrane, a polymer consisting of synthetic materials, butyl rubber.
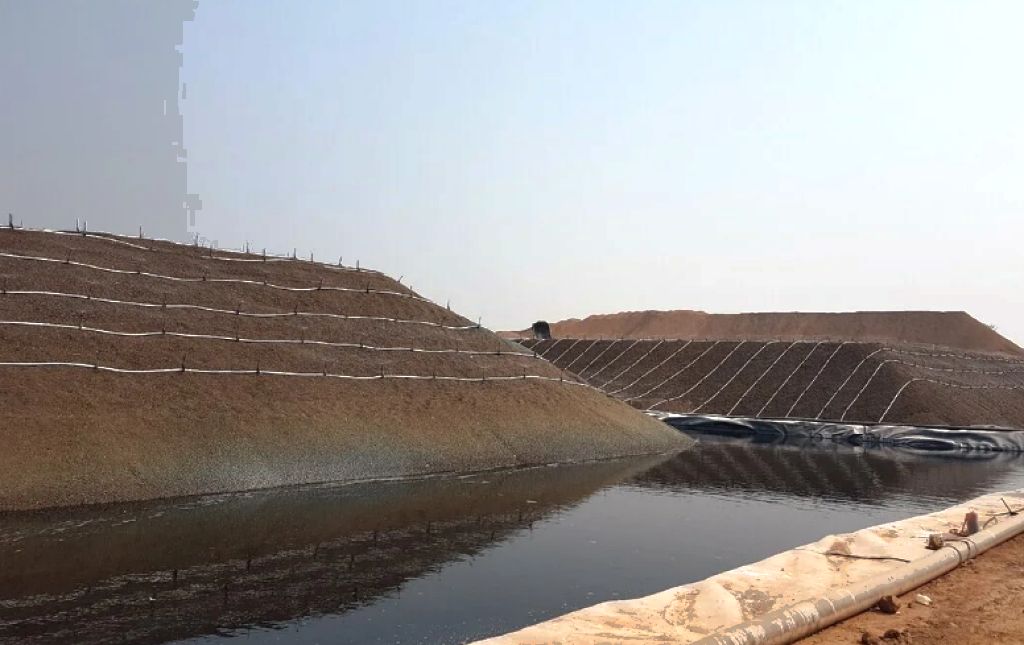
The site should be sloped 2-4 degrees, this is necessary to facilitate the drainage of residual materials. If the surface is naturally flat, it is sloped artificially. It is also important to prevent the mine from becoming weathered later on.
In addition, the site must be strong enough to hold the right amount of ore material, have a surface that is resistant to chemical attack, and be intact so that solutions do not leak out.
Stacking of ore in a heap with special equipment
The correct formation of a stack, i.e. a pile, is the most responsible stage of the technology. The success of the whole process depends on it. The stacking of the pile must be done in such a way that there are no channels in it. The content of the stack must be homogeneous, friable and porous, and this is what the screening process is for. It is important that the ore mass be permeable to the cyanides used in the leaching process.
Special equipment, bulldozers and loaders, are used to backfill the pile. The pile itself has the shape of a truncated cone up to 15 meters high. One pile can contain from 100 to 200 thousand tons.
Ore irrigation solution
Nozzles - special devices for sprinkling - are installed above the ore stacks. By means of nozzles, the piles are sprayed with cyanide solution at a rate of 0.15-3 cubic meters per square meter of ore.
The cyanide solution used has a concentration of 0.05 - 0.1 % NaCN, pH 10-11.
Drainage of mortar through the stacks (heap)
Along the sides of the stack are installed plastic-finished ditches, pipes for drainage, i.e. for filtration. The ditches are filled with drainage material: it can be the ore mass itself with excellent permeability, gravel, sand. All pipes are connected into one collector, where the gold-containing solution flows.
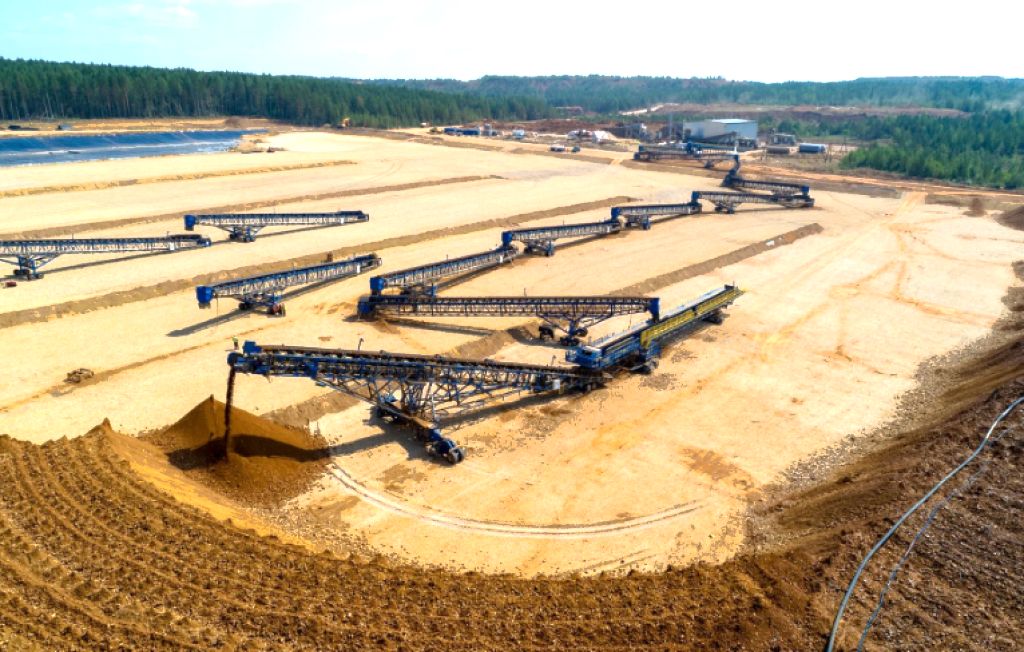
Gold leaching
Under the influence of the solvent, all gold-holding rocks are washed out. The solution containing gold descends from the top layers of the heap and flows out from under the bottom. It is collected in prepared drainage ditches, where it is cleaned of clay particles, and then sent to a common collector.
Collection of gold-containing solutions and sedimentation
Gold in solution form must be refined from ore impurities. A common method is to dissolve these impurities with acids, tin and chlorine compounds. В at home usually whitewash, aqua regia, hydrochloric acid, sodium chloride are used for this purpose. Iodide leaching is used.
In total, it takes up to 4 months to heap leach gold from ore.
Recovery of gold as cathode sludge (70-80%) or gold sludge (20-30%) by electrolysis
In order to extract gold, productive solutions after heap leaching are subjected to electrolysis. With this method, high quality gold is obtained. The process follows the formula H2AuCl4 - 4H2O. The following is used as an anode gold-containing materialobtained by heap leaching. The cathode is a gold plate. Under the influence of current the gold particles are deposited on the plate.
At the bottom of the tank where the electrolysis takes place, a sludge is deposited - the remains of the gold-containing alloy.
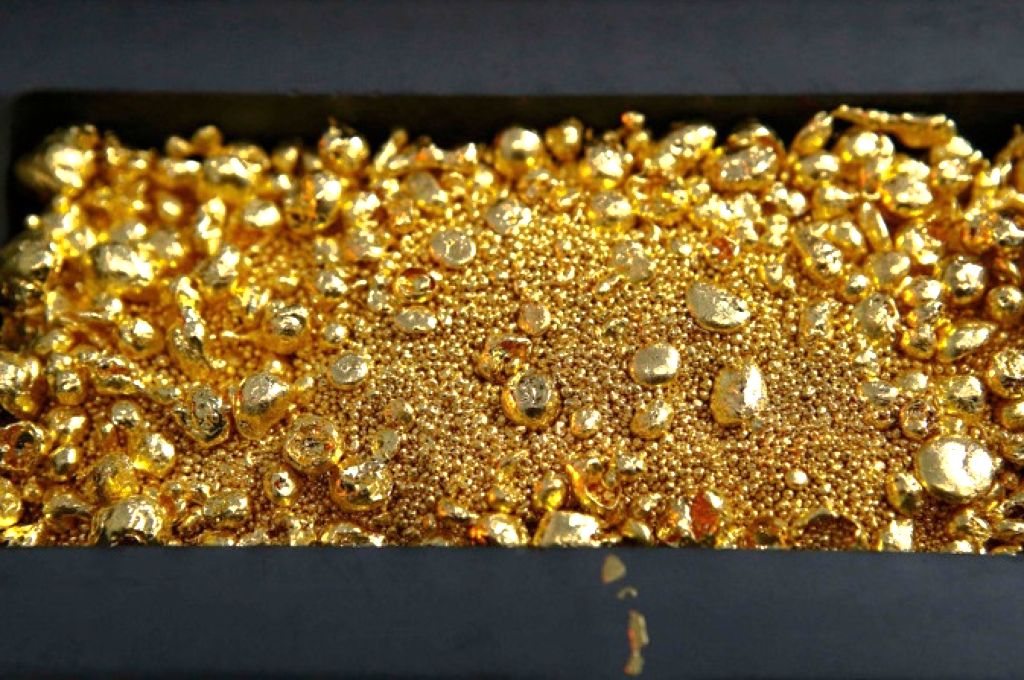
Sludge melting in a crucible or ore-thermal furnace
The cathode gold-containing residues are melted in crucible and ore-thermal furnaces in two stages:
- calcination - at this stage the material is dehydrated, base metals are oxidized, sulfides are decomposed, and carbon is burned out;
- ligature melting.
Before smelting, the gold-containing sludge is washed and degreased.
Decontamination of ore stacks
When gold is leached, harmful cyanide and heavy metals remain in the residual materials. The mine and the solutions used need to be decontaminated. This is done through biological treatment and chemical oxidation.
Oxidize processed ores with hypochlorite, sulfur dioxide, hydrogen peroxide and other substances.
Reclamation of the site and damaged soil
Environmental issues are pressing issues related to gold mining. Empty mines and unauthorized landfills remain at gold heap leach sites. Open-pit ores are a source of acids, which are leached by natural precipitation and flow into water bodies, polluting them. Therefore, according to the law, mining companies are required to build landfills. In addition, the site is transferred for biological use and reclamation activities are carried out.
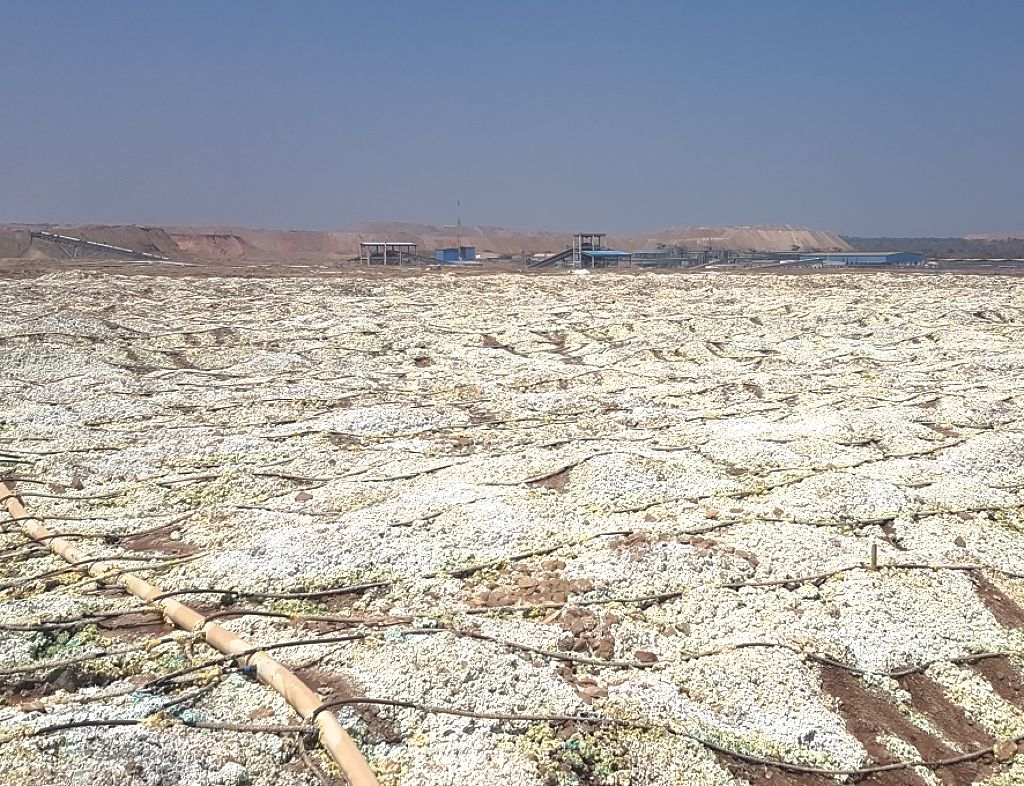
Three methods of heap leaching
There are three heap leaching methods used in industrial production. Each of them differs in the list of equipment used and the scheme of work.
The design of long-term reusable sites
This method assumes that the construction of long-term sites will be carried out. All conditions for production are created on these sites: hard waterproofing covers, technological tanks. It is assumed that such sites will be used many times.
Processed ore is removed from the process site and tailings ponds are built for this purpose.
Disposable waterproofing pads
This method is more common. Sites are built for disposable use, so soft, lower quality materials are used. The processed ore remains on site. In general, a minimum of money is spent on the construction of disposable sites.
Dump leaching with ore stacking in the form of a dam
This type of leaching takes place by so-called renewal of the stack. The heap is poured in the form of a dam. When the lower layer of ore is leached, the upper layer settles and fresh ore is poured in its place. When the process is complete, the treated material is decontaminated and reclaimed.
Video: heap leaching of gold: technology and principles of the method
Advantages and peculiarities of using methods for gold mining
Heap leaching is way to get gold in a short period of time and with minimal monetary costs. This method of gold mining has both advantages and disadvantages.
As you can see, there are few negative aspects of heap leaching. If the process is properly organized, losses will be minimal.
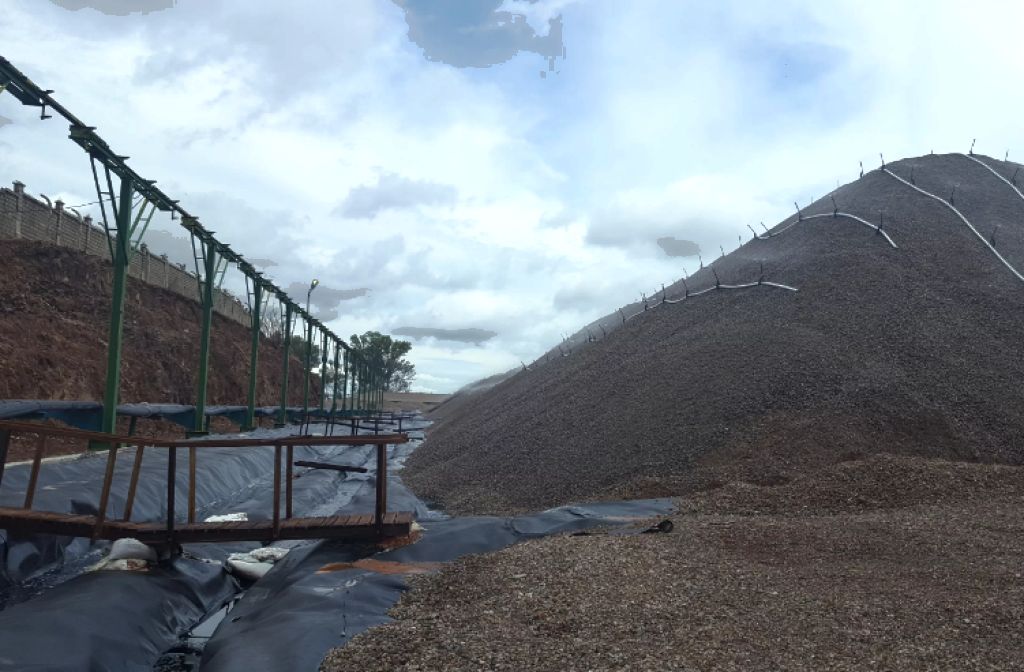
Causes of ineffective leaching process
Heap leaching technology is not always efficient or cost-effective. Typical causes of heap leach project failure:
- Weak percolation of the chemical through the heap - this may be due to the structure of the ore, for example, the presence of clay impurities. Perhaps the cause is the quality of the chemical solution, its improper concentration.
- It takes too long to get the pile into the working mode. Temperature and climate regimes are directly related to the organization of the process. Ore piles can weather, chemical reagent can evaporate under the influence of high temperatures. Frequent rains can wash all the necessary elements out of the ore, a sheltering system should be considered.
- The leaching cycle is too long. Gold-bearing ore may contain components that slow down leaching. For example, iron, lead, minerals will reduce the dissolution rate of gold. Carbonaceous minerals will react with cyanide, with the result that the latter will not perform its primary task of dissolving gold. Activated carbon has the ability to adsorb, i.e. absorb gold particles, which will also affect the leaching rate. The process is slow if the ore is not crushed enough and there are large lumps.
- Too low recovery. The percentage of gold extraction depends on the processing method of the obtained gold-bearing solution. If sedimentation is carried out using zinc, more than 800 grams of precious metal per day can not be extracted. A high level of extraction is characteristic of carbon sorption.
- Poor drainage of the leaching solution from the piles. Excess impurities and dirt are removed from the solution with the excess fluid. A poor drainage system prevents the solution from being cleaned.
As you can see, heap leaching technology is one of the most effective methods of gold mining worldwide. Many processing plants operate on three stacks at once for continuity of the process. While the first pile is poured, the second pile is leached, and the third pile is decontaminated and cleaned up.
Обязательно посмотрю…